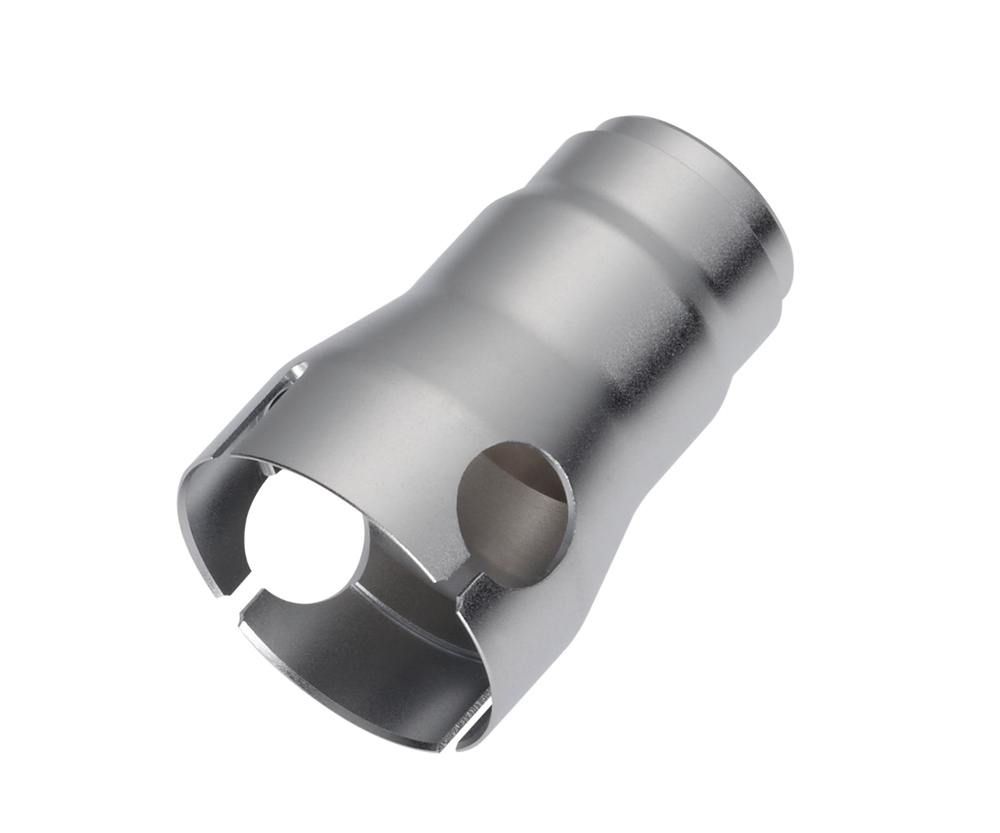
北京機械加工廠車床切削油霧潤滑技術優點和裝置
2024-04-11
北京機械加工廠絲杠加工的技術進程:
下料—校直—車端面、打基地孔—車外圓及軸頸—校直—粗銑或粗車螺紋—時效處理—校直—修正端面及基地孔—精磨外圓、軸頸—半精車螺紋、精車螺紋—校直—查驗。
假如用的是熱軋鋼,下料后還要有燜火和無心車等工序。
1、粗加工可用精度較差但生產率高的方進行
2、工序間答應屢次校直。
3、產量大時,多在立式爐內進行時效處理;產量小時,人工擊打和自然時效并用消除內應力,削減曲折變形。
精細絲杠的特色及應留意的疑問:
一、基面挑選
絲杠的首要基面為軸頸和頂尖孔,但常用頂尖孔為基面,關于長度較小的絲杠(3~4m),用頂尖最為適宜。4m以上時,通常將絲杠一端固緊在機床卡盤內,而另一端裝在特別支座的精細導套中。
1、導套的運用可削減絲杠曲折變形
2、絲杠的錐度及橢圓度在導套方位和支承長度內應不超越0.004mm,粗糙度不高于Ra0.4,與導套的合作空隙不超越0.008~0.012mm。
3、頂尖孔常會被用到,不管長短,應進行淬火和磨削,使其幾許形狀準確,表面光潔。
二、嚴格控制各工序的加工余量和切削用量
1、移動基地的辦法可削減余量,節省資料和工時,讓變形影響減到最低。
2、長度較大的絲杠,每逢高低溫時效后,有必要查看徑向跳動,找出跳動最大的當地,以這當地作為基面,用基地架支撐工件,如下圖。然后切掉上一工序留下的頂尖孔,按沿全長遍地跳動接近最大跳動量的一半為準則,從頭打頂尖孔。
3、精細絲杠不答應冷校直,會增大加工余量,所以準確的切削用量很主要。
參考切削用量:
預加工螺紋時,切削速度為2~3.5m/min,徑向進給量為0.06mm/r;
精車螺紋時,切削速度為1~1.5m/min,徑向進給量為0.02~0.04mm/r.
三、加工進程中的變形疑問
1、合理的組織時效工序,可去掉內應力,減小變形
2、熱處理時,不能用支承支住或平放絲杠,防止引起自重變形。必定要將絲杠吊起。
3、工件在機床夾持時,要防止不合理的夾持方法。像工件在機床上車完后,沒振擺,松開卡盤卻呈現。卻掉前頂尖,可削減
4、需淬硬的絲杠。淬火防止不了變形。小批量和試樣,可采用的辦法:淬火后將螺紋磨出(不預先車出)。
5、較長的絲杠,設備滿意不了。可將毛坯分成若干段,別離加工,最終精加工前安裝成一個全體,再進入最終的精加工工序。或完工后再安裝。